Selecting A Waterjet
As with any purchase, the wants and needs must be weighed with a practical eye. A variety of machines exist, yielding a number of different price levels. By closely examining your production needs and matching the machine to it, you can minimize unnecessary expenditures.
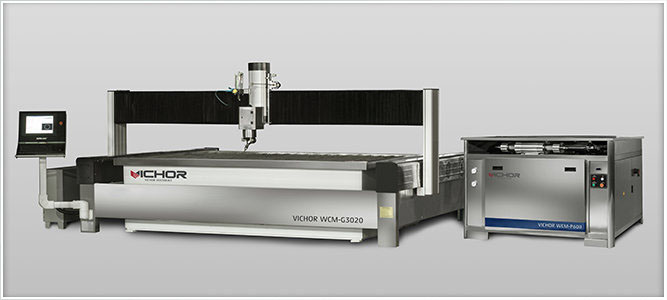
Application Workup:
Materials and thickness intended to cut with waterjet
This list suggests pump size. Parts over ½ inch thick should be cut with at least 50 HP per head. Smaller heads are more expensive per inch.
However, sometimes it can be very effective to run two small heads instead of one large head. Examining cycle times and cost per part for each configuration will help show whether one or two heads are most productive.
Stock plate sizes
Sizing a machine for an oddball large plate size can be an expensive approach. It is often cheaper to cut an oversized plate down before putting it on a waterjet, or letting the oversized plate overhang out of the catcher.
Finished part accuracy required?
As with the plate size, you should consider the majority of the work you do, not THE most accurate.
Is a 100 to 250 RMS sandblasted surface finish acceptable “as cut”?
If you do not have to perform secondary operations to obtain a very smooth surface (better than 100 RMS), then your costs per part should be quite low on a waterjet. In hard materials, like hardened steels, titanium, nickle alloys, ceramics, the roughing out of a part with a waterjet still may save significant costs, even when final finishing is required.
Operator proficiency?
Are your operators also your programmers? Is it difficult to get and to hold programmers and operators? If so, then an intelligent control will improve your productivity greatly over the more complex and hard to learn CAM to CNC based systems.
Who will perform maintenance?
If the operator is also the maintenance person, then ensure adequate training is provided. You may want to consider purchasing an additional on-site operator and maintenance training day (or two) 60 days after installation.
Will the operator run just the waterjet machine, or other machines too?
If the operator will be running more than just one machine at a time, then look into technology that aids automated operation. For example, from some manufacturers, you can purchase a cutting performance monitor that will automatically stop the machine if any deviation from peak efficiency occurs. Or, if your batch size permits, look to stack cutting. The jet on-time is extended but part production is very high. The operator can be running another machine while the jet is cutting.
Will you be nesting parts on a plate?
Many nesting packages are available. Although a generic nesting package can create a nest for a waterjet machine, it is typically understood that nesting packages (and machine tool controls) that are designed for a specific process are more powerful and easier to use than the generic, multi-process version.
Do I have the facilities?
Be prepared to discuss with the manufacturer all facilities issues. Floor space, power, water, compressed air, drainage, material storage, material loading, clean shop area for high-pressure maintenance, programming office area.